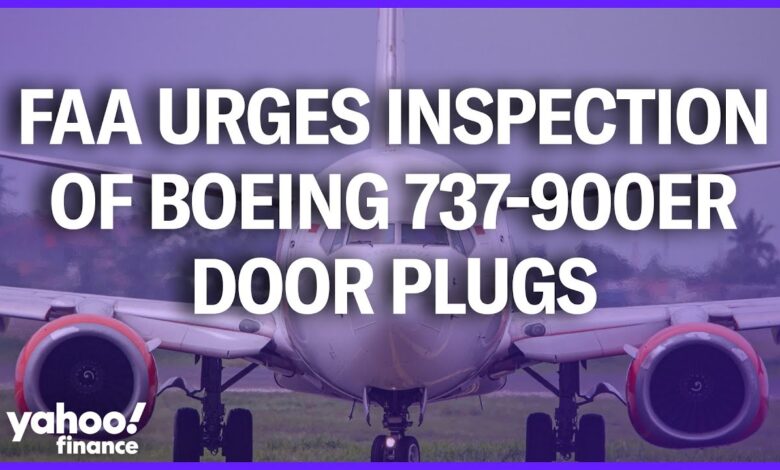
FAA Boeing 737-900ER Door Plug A Deep Dive
Faa boeing 737 900er door plug – FAA Boeing 737-900ER door plug – a crucial component for aircraft safety and maintenance. This comprehensive guide explores the intricacies of these plugs, from their function and specifications to installation, maintenance, and troubleshooting. We’ll delve into the materials, potential issues, and even future trends in door plug technology, ensuring you have a complete understanding.
Understanding the FAA Boeing 737-900ER door plug is essential for anyone involved in aircraft maintenance. This in-depth look covers everything from its role in the overall system to the steps involved in replacement and maintenance.
Overview of FAA Boeing 737-900ER Door Plug
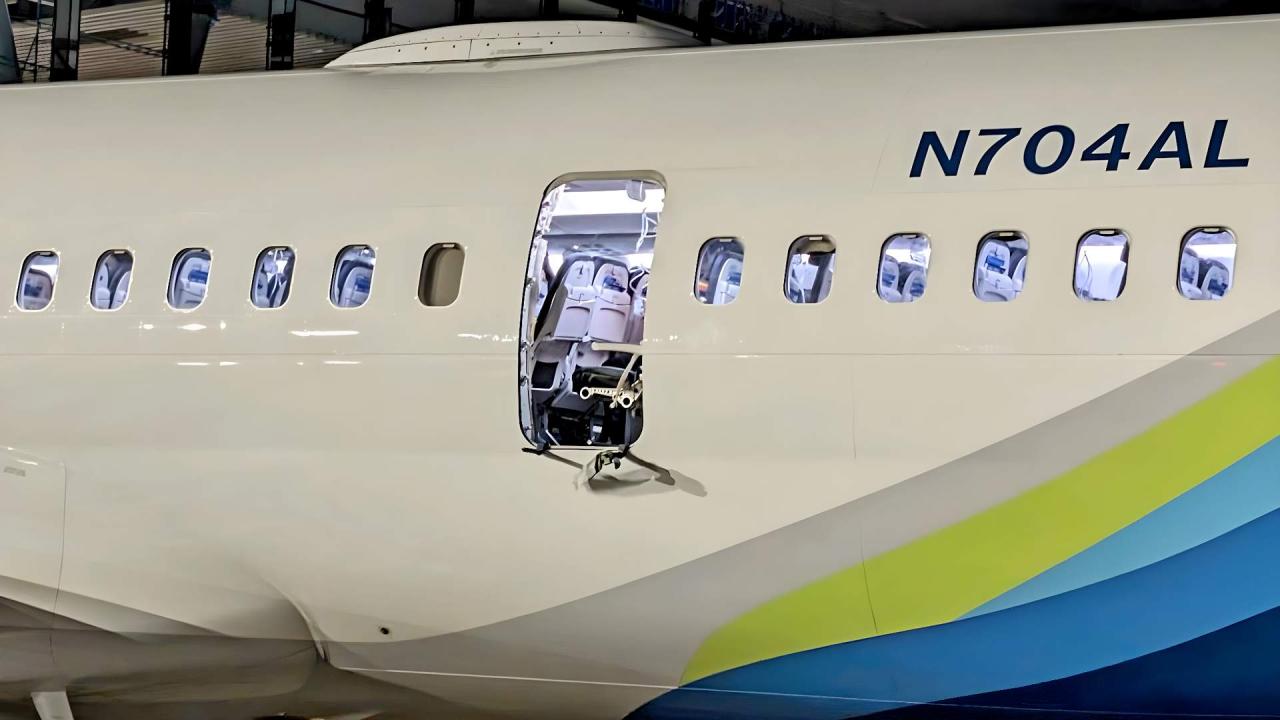
The FAA Boeing 737-900ER door plug is a crucial component ensuring the structural integrity and operational safety of the aircraft’s door system. Its design and implementation are meticulously regulated to prevent leaks, maintain air pressure, and enhance the overall performance of the aircraft. Understanding its specifications, maintenance procedures, and different types is vital for ensuring the safe operation of the aircraft.The door plug’s primary function is to seal the aircraft door opening, preventing air from escaping during flight.
This ensures the cabin maintains the correct pressure for passenger comfort and safety, and it also aids in preventing the ingress of foreign objects and moisture. The plug’s design incorporates various features to guarantee a tight seal under different flight conditions.
Purpose and Function of the Door Plug
The FAA-approved door plug for the Boeing 737-900ER plays a critical role in maintaining cabin pressure and preventing leaks. Its purpose extends beyond basic sealing; it also contributes to the aircraft’s overall structural integrity and safety. Proper installation and maintenance of the plug are paramount for preventing depressurization incidents and ensuring the safe operation of the aircraft.
Specifications and Technical Requirements
The design and manufacturing of the Boeing 737-900ER door plug adhere to stringent FAA regulations and industry standards. These standards ensure the plug’s compatibility with the aircraft’s door system and its ability to withstand the various stresses encountered during flight. Materials used must meet specific requirements for strength, durability, and resistance to environmental factors. Specific dimensions and tolerances are crucial for proper sealing and operational efficiency.
Speaking of tricky technical issues, the FAA’s Boeing 737-900ER door plug problem has been a real headache for airlines. Meanwhile, the recent Carroll verdict, especially regarding Haley Trump, is definitely causing a stir in political circles. It’s fascinating to see how these seemingly unrelated issues are playing out, all while the FAA is still working on solutions for the 737-900ER door plug – a real challenge for plane maintenance, carroll verdict haley trump.
Hopefully, this will all get sorted out soon and the airlines can get back on track.
Importance of Door Plug Maintenance, Faa boeing 737 900er door plug
Regular maintenance of the door plug is critical for preserving the aircraft’s operational safety. This includes visual inspections to identify any signs of damage, wear, or deterioration. Proper maintenance ensures the plug continues to function as intended, maintaining the integrity of the aircraft’s door system and the safety of its occupants. Failure to maintain the door plug could lead to serious operational issues, including depressurization, and compromise the overall safety of the aircraft.
Ever wondered about the FAA Boeing 737-900ER door plug? It’s a fascinating piece of aircraft engineering, but did you know its importance extends beyond the mechanics? Recent discussions about the Olympic intersex athlete Maximila Imali, Olympic intersex maximila imali , have sparked wider conversations about inclusivity and fair play. This parallels the crucial role of FAA standards in ensuring safety and fairness across various facets of aviation, including the exact specifications for a 737-900ER door plug.
It’s all interconnected in a fascinating way.
Types of Door Plugs for the Boeing 737-900ER
Different types of door plugs may be employed, depending on the specific configuration and operational needs of the aircraft. The selection of the appropriate plug type is crucial for optimal performance.
Plug Type | Material | Size | Application |
---|---|---|---|
Standard Seal Plug | High-strength rubber or elastomer | Variable, depending on door size | General use for most flight conditions |
Emergency Seal Plug | High-strength reinforced composite material | Variable, depending on door size | Used in emergency situations or when the standard plug is damaged |
High-Pressure Seal Plug | Special composite material with high tensile strength | Variable, depending on door size | Used for extended flight periods or high-altitude flights |
The table above Artikels various door plug types, highlighting the materials used, sizes, and applications. Each type is designed to meet specific operational needs and is crucial in maintaining cabin pressure.
Installation and Replacement Procedures
Installing and replacing door plugs on a Boeing 737-900ER requires meticulous attention to detail and adherence to strict procedures to ensure safety and structural integrity. Proper installation prevents leaks, maintains airtight seals, and preserves the aircraft’s overall operational efficiency. Failure to follow these procedures can lead to costly repairs, safety hazards, and potential operational disruptions.
Installation Steps for a New Door Plug
This section details the essential steps involved in installing a new door plug on a Boeing 737-900ER. Adherence to these steps is crucial for a successful and safe installation.
- Preparation is Key: Thoroughly inspect the door plug’s mating surface for any damage, debris, or corrosion. Ensure the area is clean and free of contaminants that could hinder proper seal formation. Use appropriate cleaning agents and procedures as Artikeld in the maintenance manual.
- Alignment and Positioning: Precise alignment of the new door plug is paramount. Refer to the aircraft’s technical documentation for precise measurements and guidelines. Employ specialized tools for precise positioning and secure the plug into place using designated fasteners. Incorrect alignment could lead to leaks or premature wear.
- Torque and Tightening Procedures: Apply the correct torque to all fasteners. Over-tightening can damage the surrounding components. Under-tightening could compromise the seal and lead to leaks. Use calibrated torque wrenches and adhere to the manufacturer’s specifications.
- Seal Verification: After installation, visually inspect the seal for any gaps or irregularities. Pressurize the area, if applicable, to verify the integrity of the seal. Listen for any unusual noises or signs of leakage. Any indication of leaks necessitates immediate remedial action.
Replacement of a Damaged or Worn-out Door Plug
Replacing a damaged or worn-out door plug is a critical maintenance task. Careful execution of these steps prevents potential issues and ensures a functional seal.
- Assessment and Documentation: Thoroughly document the condition of the damaged plug and the surrounding components. Note any visible damage or signs of wear. This documentation is vital for tracking maintenance and for future reference.
- Removal Procedure: Carefully remove the damaged door plug, adhering to the appropriate procedures. Use specialized tools to prevent damage to the surrounding structure. Check the condition of the fasteners and surrounding areas during removal. Any signs of further damage warrant immediate attention.
- Inspection of the Mounting Surface: Examine the mounting surface for any damage, corrosion, or debris. Clean the surface thoroughly to ensure proper adhesion of the new plug. Any significant damage to the mounting surface will require repair before installing a new plug.
- Installation of the New Plug: Follow the installation steps Artikeld in the previous section for a new door plug. This includes proper alignment, torque application, and seal verification.
Comparison of Installation Methods
Different installation methods might be employed for various aircraft or specific circumstances. The choice of method hinges on the complexity of the job, the availability of tools, and the safety considerations.
Ever wondered about the FAA’s stance on Boeing 737-900ER door plugs? It’s a fascinating area of aviation safety, but sometimes, it’s hard to connect these seemingly niche details to broader political and economic landscapes. For instance, the recent push for infrastructure improvements in Wisconsin, as detailed in this article about Biden taking on Trump’s policies taking on trump biden promotes infrastructure decade in wisconsin , could potentially impact future aviation regulations.
Ultimately, these intricate parts of the 737-900ER door plug system are essential for the safe operation of commercial aircraft.
Installation Method | Pros | Cons |
---|---|---|
Manual Installation | Simple and cost-effective for straightforward installations. | Potential for inaccuracies in alignment and torque application if not properly executed. |
Hydraulic Installation | Greater precision in alignment and torque application, minimizing human error. | Requires specialized equipment and trained personnel, increasing the overall cost. |
Routine Maintenance Inspection Procedure
Regular inspection of the door plug is crucial for preventing potential issues. The following procedure Artikels a thorough inspection process during routine maintenance.
- Visual Inspection: Carefully examine the door plug for any signs of damage, such as cracks, corrosion, or deformation. Look for any debris or foreign objects that could compromise the seal.
- Seal Verification: Visually inspect the seal for any gaps, irregularities, or signs of wear. If necessary, use a pressure test to confirm the seal’s integrity.
- Fastener Inspection: Check all fasteners for proper tightening and secure attachment. Note any loose or corroded fasteners and address them promptly.
- Surrounding Area Inspection: Inspect the area surrounding the door plug for any signs of damage or wear that could affect the plug’s performance.
Materials and Components
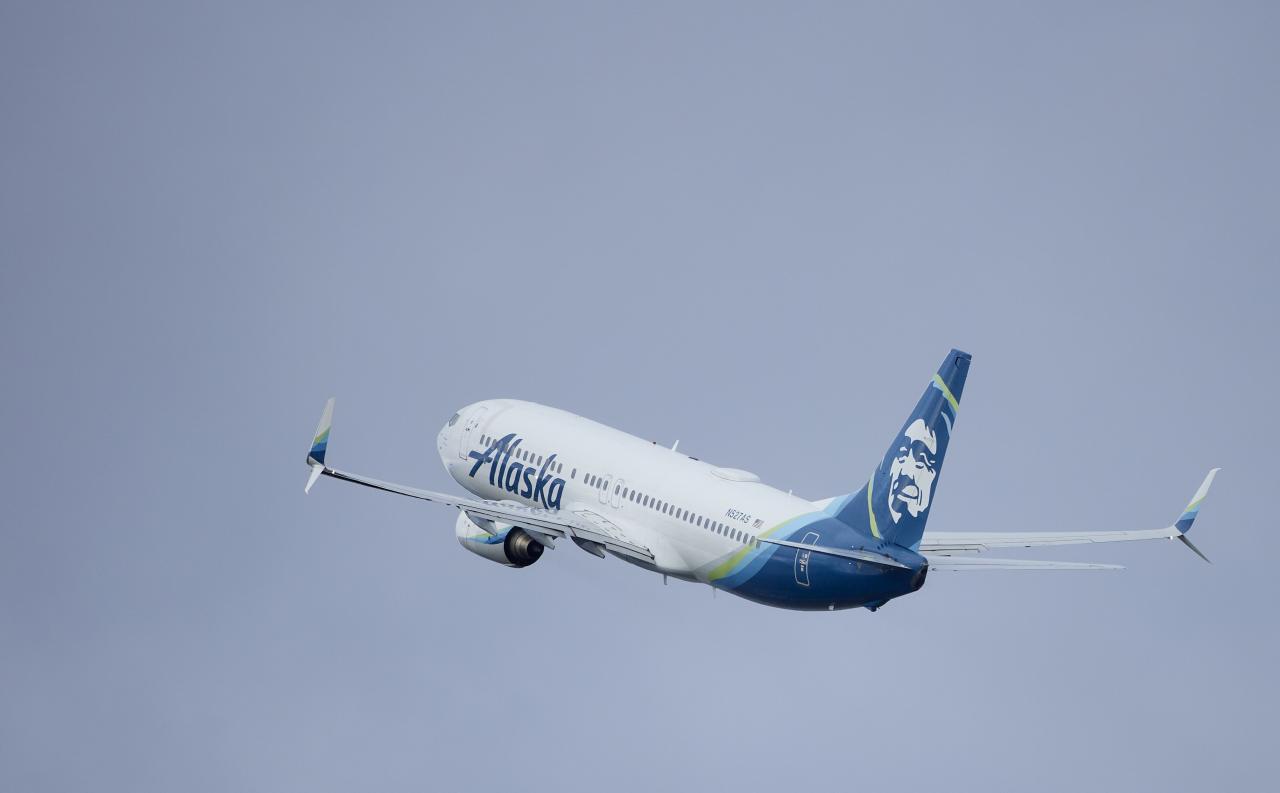
Aircraft door plugs are crucial components ensuring the structural integrity and safety of the aircraft’s fuselage. Proper selection and installation of these plugs are vital for maintaining operational efficiency and preventing potential hazards. This section delves into the materials, components, and quality control measures associated with Boeing 737-900ER door plugs.The materials used in aircraft door plugs are carefully chosen to meet stringent requirements.
These materials must possess exceptional durability, resistance to wear, and environmental factors. Different materials exhibit varying degrees of these properties, impacting the overall performance and lifespan of the plug.
Common Materials and Their Properties
Aircraft door plugs often utilize materials like aluminum alloys, stainless steel, and composite materials. Aluminum alloys are commonly used due to their lightweight nature, which contributes to the overall aircraft weight. Their excellent corrosion resistance and formability make them suitable for the application. Stainless steel, known for its high strength and resistance to corrosion, is sometimes employed in areas where higher strength is needed or in environments with harsh conditions.
Composite materials, offering a combination of strength and light weight, are also becoming increasingly popular, particularly in areas where weight reduction is critical.
Comparison of Material Performance
The performance of different materials in door plugs is evaluated based on several key factors. Durability is assessed by testing the material’s resistance to fatigue and repeated stress. Resistance to wear considers the material’s ability to withstand abrasion and friction from the environment. Environmental impact, encompassing factors like corrosion resistance and chemical resistance, is also a crucial consideration.
For example, aluminum alloys generally exhibit high resistance to corrosion, making them suitable for diverse environments. Stainless steel excels in harsh conditions, while composite materials, depending on their composition, can offer superior resistance to specific types of wear and tear.
Door Plug Assembly Components
The door plug assembly is a complex system comprising various components working together. This includes fasteners, seals, and gaskets, each playing a specific role in ensuring the plug’s proper function and the aircraft’s safety.
- Fasteners: These components secure the door plug to the fuselage. Common types include rivets, bolts, or specialized fasteners designed for aircraft applications. The selection of fasteners depends on the specific design and loading conditions.
- Seals: Seals are crucial for preventing leakage and maintaining the integrity of the aircraft’s cabin pressure. Materials like elastomers or specialized sealants are employed. The seal’s design and material must withstand the pressure differentials and environmental conditions.
- Gaskets: Gaskets play a vital role in creating a tight seal between the door plug and the fuselage. They are designed to compensate for variations in the surface and maintain a reliable seal. Gaskets often utilize materials like rubber or other resilient compounds.
Quality Control Measures
Rigorous quality control measures are implemented throughout the manufacturing process to ensure the reliability and safety of door plugs. These measures are essential for maintaining the aircraft’s structural integrity.
- Material Inspection: Materials are inspected for defects and adherence to specified tolerances. This includes checking for impurities, dimensional accuracy, and adherence to material specifications.
- Component Testing: Components like seals, gaskets, and fasteners are subjected to rigorous testing to ensure their performance under various conditions. This may include pressure tests, vibration tests, and fatigue tests.
- Assembly Verification: The assembly process is monitored to ensure adherence to established procedures. This includes verifying the correct installation of components and adherence to torque specifications.
Troubleshooting and Maintenance
Maintaining the integrity of the Boeing 737-900ER door plugs is crucial for aircraft safety and operational efficiency. Proper troubleshooting and preventative maintenance minimize the risk of leaks, malfunctions, and potential damage, ultimately extending the lifespan of these critical components. Addressing issues promptly and effectively reduces downtime and ensures compliance with FAA regulations.
Common Issues
The Boeing 737-900ER door plugs, like any mechanical component, are susceptible to various issues. Common problems include leaks, resulting from damaged seals or improper installation. Malfunctions, such as failure to properly seal or deploy, can also occur due to electrical or mechanical system errors. Furthermore, physical damage, from impacts or harsh environmental conditions, can compromise the integrity of the door plug, leading to structural issues.
Troubleshooting Steps
A systematic approach to troubleshooting is essential for efficient issue resolution. Initial steps involve visual inspection for signs of damage, such as cracks, dents, or missing components. Subsequent steps include checking for leaks by using pressure testing methods. These methods involve carefully applying pressure to the door plug and observing for any leakage. If leaks are detected, the specific location of the leak should be pinpointed to identify the source of the problem.
Malfunctions often manifest as abnormal operation, such as erratic deployment or failure to seal. Diagnostic tools and procedures, specific to the door plug model, are used to pinpoint the root cause of the malfunction. In the event of physical damage, the affected area is carefully assessed to determine the extent of the damage and the required repair or replacement procedures.
Preventative Maintenance
Preventative maintenance significantly extends the lifespan of the door plugs. Regular inspections, performed according to established schedules, are critical for detecting potential issues before they escalate. Inspections should include visual checks for signs of wear, damage, or corrosion. These visual inspections should be meticulously documented for future reference. Routine lubrication of moving parts, if applicable, ensures smooth operation and prevents friction-related damage.
Furthermore, proper storage and handling procedures, adhering to manufacturer guidelines, can prevent accidental damage. Environmental factors such as extreme temperatures or humidity can affect the performance of the door plugs. Storing the door plugs in controlled environments, within the specified temperature and humidity ranges, can help maintain their integrity.
Documentation Procedures
Comprehensive documentation is crucial for maintaining a record of maintenance activities. A dedicated logbook should be maintained to record all inspections, repairs, and replacements of the door plug. Each entry should include the date, time, technician’s signature, and a detailed description of the work performed. Any deviations from standard procedures should be clearly documented. Detailed photographs or diagrams can help illustrate the specific conditions of the door plug.
Records should also include the part number, serial number, and any relevant maintenance manuals or specifications. This detailed documentation will serve as a valuable reference for future troubleshooting and maintenance activities. Such documentation is essential for compliance with FAA regulations and for ensuring the aircraft’s operational safety and efficiency.
Regulatory Compliance and Safety Standards
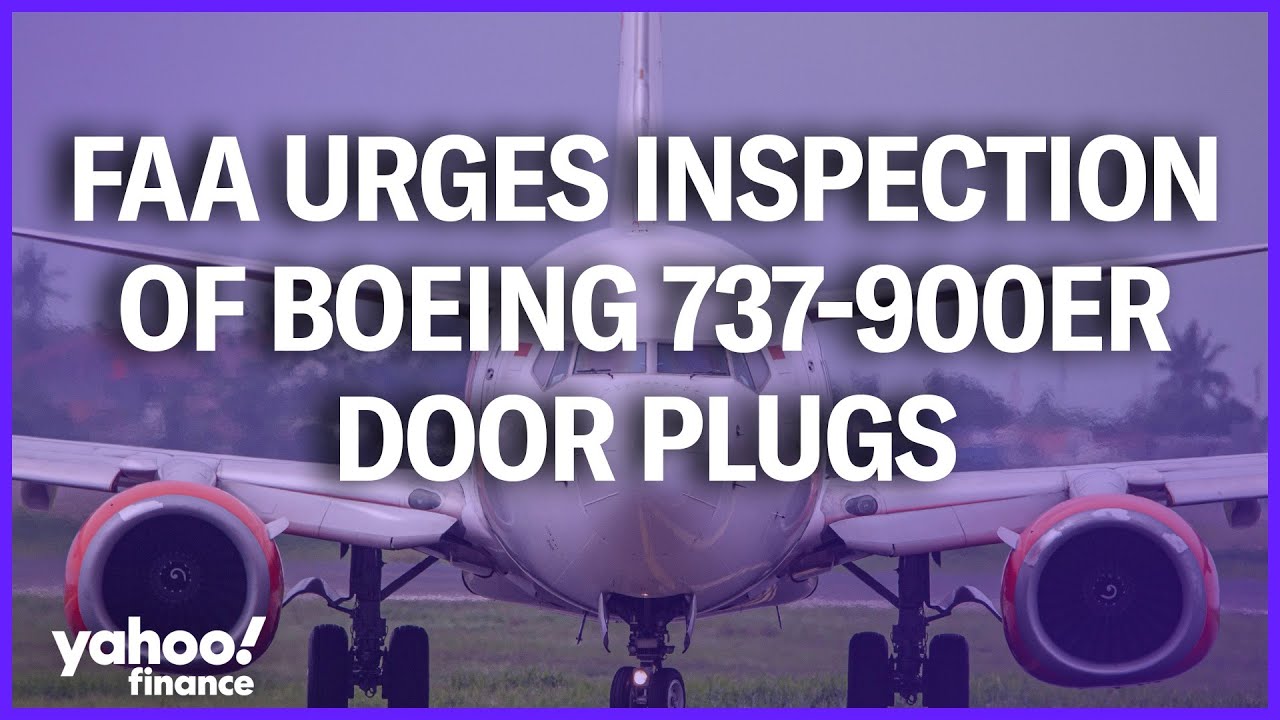
Ensuring the safety and integrity of aircraft components is paramount, and door plugs on the Boeing 737-900ER are no exception. Adherence to FAA regulations and standards is crucial for maintaining the structural integrity and operational safety of the aircraft. These standards dictate the specific requirements for installation, inspection, and maintenance of these vital components.The FAA sets forth a comprehensive framework of regulations and standards to guarantee the safety of aircraft operations.
These regulations encompass all aspects of aircraft design, manufacturing, maintenance, and operation. Failure to comply with these regulations can lead to significant safety risks, potentially resulting in accidents or incidents.
The FAA’s investigation into the Boeing 737-900ER door plug issue is ongoing, but it’s worth noting that recent news about Chris Young’s charges being dropped ( chris young charges dropped ) might have some interesting, albeit indirect, implications for the overall safety concerns surrounding the plane’s design. Hopefully, this won’t further delay the FAA’s decision on the 737-900ER door plug issue, and we can get back to focusing on the core problem of potential safety hazards.
FAA Regulations and Standards for Boeing 737-900ER Door Plugs
The FAA’s regulations, including but not limited to 14 CFR Part 43, 14 CFR Part 91, and other relevant documents, provide the guidelines for maintaining and operating aircraft. Specific sections detail the required maintenance procedures for door plugs, emphasizing the importance of adhering to these regulations for ensuring the structural integrity of the aircraft.
Inspection Procedures for Door Plugs
Regular inspections are essential for identifying potential issues with door plugs before they escalate into safety hazards. These inspections typically include visual checks for damage, wear, and proper installation. Detailed records of inspections must be maintained, providing a historical record of the door plug’s condition over time.
Ever wondered about the FAA Boeing 737-900ER door plug? It’s a crucial component, but the extreme cold conditions affecting snow polo in St. Moritz, due to climate change, potentially impacting the design and testing of these parts in the future. The delicate balance of materials and engineering required for the 737-900ER door plug, thus, needs careful consideration as global warming continues to impact everything, from extreme weather to the components of our airplanes.
Inspection Checklist for Door Plugs
A comprehensive checklist ensures thorough inspections. This checklist should cover the following:
- Visual inspection for any signs of damage, cracks, or corrosion.
- Confirmation of proper seating and secure attachment to the aircraft structure.
- Assessment of any wear or degradation of the sealing material.
- Verification of correct torque levels for mounting hardware.
- Examination of the plug’s surrounding areas for potential contaminants or debris.
Potential Safety Hazards of Improperly Maintained Door Plugs
Improperly installed or maintained door plugs pose significant safety hazards. These hazards include:
- Structural Integrity Issues: Damage or wear to the plug can compromise the structural integrity of the aircraft door, leading to potential structural failures during flight.
- Leakage and Intrusion: Loose or damaged plugs can allow for the intrusion of foreign objects, or the leakage of fluids into the aircraft, posing safety and operational risks.
- Operational Disruptions: Improper sealing or maintenance can lead to operational issues, such as reduced cabin pressure or environmental hazards, jeopardizing the safety and comfort of passengers and crew.
Maintenance and Replacement Procedures
Maintenance and replacement procedures for door plugs must adhere strictly to the manufacturer’s specifications and FAA regulations. This ensures the safety and reliability of the aircraft. Detailed procedures should be documented and readily available to maintainers.
Alternatives and Future Trends
The Boeing 737-900ER door plug design, while effective, presents opportunities for improvement in cost-effectiveness, sustainability, and performance. Exploring alternatives and incorporating emerging technologies can lead to significant advancements in future aircraft designs, potentially reducing maintenance costs and environmental impact. This section examines potential alternatives, emerging technologies, and the cost-effectiveness comparison of various door plug materials and designs.
Potential Alternatives to Current Design
The current design of the Boeing 737-900ER door plug likely balances various factors, but alternative designs might offer improved performance. A key consideration is material selection, as different materials exhibit varying degrees of durability, resistance to wear, and cost. Lightweight, high-strength composite materials, for example, could reduce weight and improve fuel efficiency. Another approach is to explore designs that require less maintenance or can be more easily repaired.
Emerging Technologies for Door Plug Design
Several emerging technologies could revolutionize door plug design. Advanced composite materials, such as carbon fiber-reinforced polymers (CFRP), are gaining traction for their high strength-to-weight ratio and corrosion resistance. Self-healing materials could potentially repair minor damage automatically, reducing maintenance needs and downtime. Smart materials, which adapt to environmental conditions, could optimize performance in diverse operating environments.
Cost-Effectiveness Comparison of Materials and Designs
The cost-effectiveness of various door plug materials and designs depends on numerous factors. While a high-strength composite material like CFRP might offer superior performance, its initial cost could be higher compared to traditional materials. However, reduced maintenance costs and potential fuel savings over the aircraft’s lifespan might offset the higher initial investment. Lifecycle cost analysis is crucial for evaluating the true cost-effectiveness of different alternatives.
For example, a study by Boeing might demonstrate that using a self-healing polymer could lead to lower maintenance costs over the 20-year lifespan of the aircraft, despite an initial price premium.
Summary of Potential Improvements and Advancements
Potential improvements and advancements in door plug technology could include:
- Employing advanced composites for enhanced strength and reduced weight.
- Integrating self-healing properties to minimize maintenance requirements.
- Utilizing smart materials for adaptive performance in diverse environments.
- Developing modular designs for easier repair and replacement.
- Implementing advanced manufacturing techniques for increased efficiency and reduced costs.
These advancements are expected to lead to more robust, durable, and cost-effective door plug designs, ultimately improving the overall performance and safety of the Boeing 737-900ER.
Visual Representation
Taking a closer look at the Boeing 737-900ER door plug, visualization becomes crucial for understanding its intricate design and proper maintenance. Visual aids, from detailed diagrams to step-by-step installation images, facilitate comprehension and ensure accurate procedures are followed. This section provides a visual representation of the door plug’s inner workings, components, installation, and damage scenarios.
Internal Structure of a Boeing 737-900ER Door Plug
The Boeing 737-900ER door plug features a complex internal structure designed for sealing and preventing leaks. A key component is a resilient sealing gasket, typically made of a high-performance elastomer, ensuring a tight seal around the door opening. Reinforcing rings and structural supports provide rigidity and maintain the door plug’s integrity under various flight conditions. A robust locking mechanism secures the plug in place, preventing accidental dislodgement.
A series of internal channels and passages facilitate proper drainage and airflow.
Components of the Door Plug Assembly
A detailed breakdown of the door plug assembly reveals a variety of components working in harmony. The primary components include the sealing gasket, made of a specialized rubber compound with excellent resilience and dimensional stability. Reinforcing rings provide structural integrity to the plug, preventing deformation under pressure. A locking mechanism ensures secure attachment, preventing accidental opening. Fasteners, like screws or rivets, are vital for securing the plug to the aircraft frame.
Supporting brackets and guides aid in alignment and positioning.
Steps Involved in Installing a New Door Plug
Proper installation of a new door plug is essential for maintaining aircraft integrity and operational safety. The process involves precise alignment of the plug with the aircraft frame, ensuring a secure and leak-proof seal. Carefully applying the sealant around the perimeter of the plug, according to manufacturer specifications, is critical for achieving a leak-proof seal. Tightening the locking mechanism and fasteners in accordance with torque specifications is crucial for a stable fit.
Visual inspection of the completed installation ensures proper alignment and secures operation.
Damaged Door Plug and Repair Areas
Visual identification of damage is critical for proper repair. A damaged door plug may exhibit signs of cracking or deformation in the sealing gasket. Corrosion or wear on the locking mechanism or fasteners may be visible. Structural damage to the supporting brackets or reinforcing rings is also a concern. The damaged areas identified require specific repair procedures and may involve replacement of the entire plug or individual components.
Ending Remarks
In conclusion, the FAA Boeing 737-900ER door plug is a vital safety component requiring meticulous maintenance and adherence to regulations. This guide has provided a thorough overview, touching on everything from its crucial role in aircraft safety to the intricate details of installation and troubleshooting. By understanding the intricacies of this part, we can ensure the safe and reliable operation of these critical aircraft.
FAQ Overview: Faa Boeing 737 900er Door Plug
What are the common materials used for Boeing 737-900ER door plugs?
Common materials include aluminum alloys, stainless steel, and various composite materials, each with specific properties related to durability and resistance to wear.
What are the potential safety hazards of improperly installed or maintained door plugs?
Improper installation or maintenance can lead to leaks, malfunctions, and potential structural issues, endangering the aircraft and its occupants. Proper inspection and adherence to FAA standards are critical.
How often should the door plug be inspected during routine maintenance?
Inspection schedules vary depending on factors like flight hours and environmental conditions. Consult the relevant FAA maintenance manuals for specific guidelines.
What are the different types of door plugs available for the Boeing 737-900ER?
Various types cater to specific applications and needs, differing in materials, sizes, and functionalities. A table in the main article details these types.