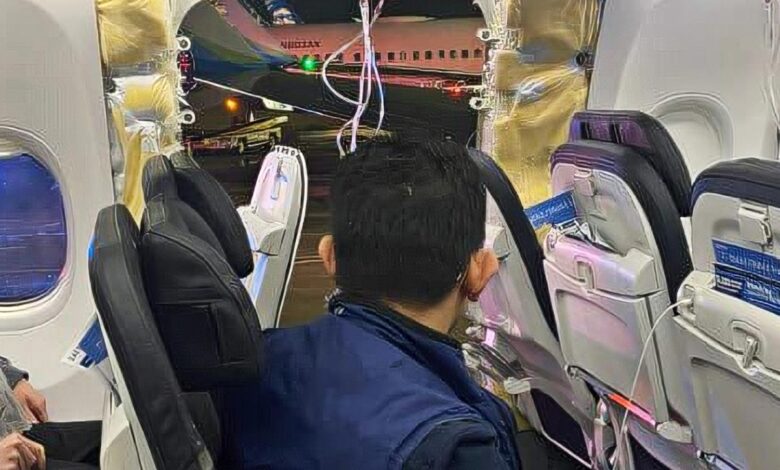
Boeing 737 Max 9 Inspections Delayed
Boeing 737 Max 9 inspections delayed, creating ripples throughout the aviation industry. This delay, stemming from a variety of factors, is causing significant disruptions to airline operations and raises important safety concerns. The intricacies of the inspection process and the potential impact on the 737 Max 9 fleet will be explored in detail.
The Boeing 737 MAX 9, a derivative of the popular 737 MAX family, was designed for efficiency and range. Its introduction promised improved fuel efficiency and reduced operating costs for airlines. However, the recent delays in inspections highlight the complex and often unpredictable nature of modern aircraft maintenance.
Background on Boeing 737 MAX 9
The Boeing 737 MAX 9, a derivative of the highly successful 737 MAX family, represents a significant evolution in the single-aisle jetliner market. This aircraft, designed for increased passenger capacity and efficiency, aimed to compete effectively in the increasingly competitive air travel sector. Its introduction marked a crucial moment in commercial aviation’s pursuit of improved performance and fuel efficiency.The 737 MAX 9’s development was driven by the need to accommodate growing passenger demand while reducing operating costs.
Key features included enhanced aerodynamics, improved engines, and advanced flight control systems, contributing to improved fuel efficiency and a more comfortable passenger experience. This model, while sharing the core architecture with other 737 MAX variants, optimized these elements for its specific design specifications.
Boeing 737 MAX 9 History
The Boeing 737 MAX 9 program commenced in the early 2010s, part of a broader initiative to modernize the venerable 737 family. Early development focused on incorporating advanced technologies to improve fuel efficiency, reduce operating costs, and enhance passenger comfort. Significant design changes included the incorporation of new engines and aerodynamic improvements, reflecting the evolving standards in aircraft design.
Timeline of the 737 MAX Program
The 737 MAX program, encompassing multiple variants like the 737 MAX 8, 9, and 10, underwent several key milestones. These included design reviews, prototype testing, and extensive flight testing to validate the aircraft’s performance in various conditions. Initial certification processes, regulatory approvals, and the aircraft’s eventual entry into service were also critical stages.
Regulatory Framework for Aircraft Inspections and Maintenance, Boeing 737 max 9 inspections delayed
The safety of commercial aircraft is paramount, and stringent regulations govern every aspect of their operation, including inspections and maintenance. International standards, like those set by the International Civil Aviation Organization (ICAO), provide a global framework for aircraft safety and maintenance practices. National aviation authorities, like the Federal Aviation Administration (FAA) in the United States and equivalent agencies in other countries, enforce these standards, ensuring compliance with safety protocols.
The Boeing 737 Max 9 inspections are, understandably, causing a bit of a stir. It’s a complex issue, and while safety is paramount, it’s worth considering the broader context. Recent headlines about the 737 Max 9 delays got me thinking about the fascinating crossover between popular culture and aviation, like the strange intersection of Godzilla, Oppenheimer, and Heron Boy in the news.
godzilla oppenheimer heron boy makes you wonder if the meticulousness of these inspections is even remotely comparable to the sheer, unstoppable force of nature. Hopefully, the delays won’t lead to further issues down the line with the Boeing 737 Max 9.
- ICAO Standards: ICAO sets out the general principles and minimum standards for aircraft maintenance and inspections, aiming for consistent global safety practices. These standards cover everything from the initial design to the ongoing maintenance and inspection procedures throughout the aircraft’s operational life.
- FAA Regulations: The FAA, in the US, provides specific regulations and guidelines for implementing ICAO standards. They Artikel detailed procedures for aircraft inspections, maintenance checks, and the use of specific technologies to ensure the safety of US-based operations. These regulations are enforced rigorously to maintain a high level of air safety.
- Maintenance Schedules: Aircraft maintenance is scheduled based on flight hours, cycles, and other factors. These schedules, meticulously documented, ensure that critical components are inspected and replaced at appropriate intervals to prevent potential failures and maintain structural integrity.
Maintenance and Inspection Procedures
Aircraft inspections follow detailed procedures. These procedures encompass visual inspections, non-destructive testing, and more advanced diagnostic tools to detect potential damage or deterioration. Rigorous documentation is crucial for tracking maintenance activities, ensuring transparency and traceability. Detailed records and documentation provide a clear audit trail of inspections, repairs, and modifications, enabling regulatory bodies to assess compliance.
Importance of Inspections
Routine inspections are critical for maintaining aircraft safety. They help identify potential issues early, preventing more serious problems and reducing the risk of accidents. Thorough inspections contribute to aircraft longevity and reliability. The cost-effectiveness of preventative maintenance, in the long run, is a significant factor in keeping aircraft operational and safe.
Reasons for Inspections Delays
The Boeing 737 MAX 9, a derivative of the popular 737 MAX family, has experienced delays in its inspection process. Understanding the underlying causes is crucial for assessing the impact on safety and production schedules. These delays are not isolated incidents; they are part of a broader pattern of challenges facing the aerospace industry.The complex nature of aircraft inspections, coupled with the intricate design of the 737 MAX 9, contributes significantly to the observed delays.
Boeing 737 Max 9 inspections are reportedly delayed, adding another layer of complexity to the ongoing saga. While the reasons behind these delays remain unclear, it’s worth considering the wider implications, such as the potential impact on air travel schedules and passenger safety. Learning about naming conventions for babies, like how the apellido bebe madre padre system works, might seem far removed from aircraft maintenance, but the intricate details of every system have a role to play in the bigger picture.
Ultimately, these delays raise questions about the thoroughness of safety procedures and their compliance with regulations.
Factors such as the need for rigorous testing, meticulous documentation, and the identification of potential issues at various stages of the inspection process, are critical in maintaining safety standards.
Potential Contributing Factors to Delays
Several factors can contribute to delays in the inspection process. Supply chain disruptions, exacerbated by global events, can affect the timely availability of parts and materials required for inspections. This is a recurring theme in various industries, impacting production timelines and project completion. Further, stringent regulatory requirements necessitate comprehensive testing and documentation, leading to longer inspection times.
The intricate design of the 737 MAX 9, with its specific structural components and functionalities, contributes to the need for more thorough inspections compared to simpler designs, adding complexity and time.
Comparison of Inspection Procedures
The inspection procedures for the 737 MAX 9 differ from those of other Boeing models due to its unique design features. The MAX 9’s advanced aerodynamic features, for example, require specific inspection protocols to ensure optimal performance and longevity. The addition of new technologies and materials in the MAX 9 introduces the need for new testing methodologies and specialized personnel.
The delayed Boeing 737 Max 9 inspections are causing a ripple effect, impacting everything from airline schedules to the overall aviation industry. This isn’t just about airplane parts, though. The recent Biden veto of the Republican electric vehicle charging bill biden veto republican electric vehicle charging highlights a broader conversation about priorities and investment. Ultimately, these seemingly disparate issues point back to the critical need for thorough and timely inspections on the 737 Max 9 to ensure safety for passengers and crew.
Comparison to older models reveals variations in the scope and depth of inspections, with the MAX 9 requiring more rigorous assessments to accommodate the evolving safety standards and technological advancements.
Identifying and Resolving Issues During Inspection
A robust procedure for identifying and resolving issues during the inspection process is crucial for aircraft safety. A standardized checklist is used for each inspection, guiding inspectors through the various components and functionalities. This ensures that no critical element is overlooked. When discrepancies are found, a detailed report is generated, outlining the nature of the issue, its potential impact, and proposed solutions.
This report is crucial for effective communication and collaboration between engineers, technicians, and management. The procedures involve collaboration among different teams to ensure that the identified issues are properly documented and resolved.
Impact of Component Failures or Defects
Component failures or defects, if left undetected, can have significant impacts on the structural integrity of the aircraft. A compromised component could lead to unforeseen stress on other structural elements, potentially jeopardizing the safety of the aircraft during flight. Real-world examples of component failures in similar aircraft underscore the critical need for rigorous inspections. The consequences of such failures can range from minor inconveniences to catastrophic failures, highlighting the importance of meticulous inspections.
The delayed inspections on the Boeing 737 Max 9 are causing quite a stir, and rightfully so. Safety is paramount, and these delays highlight the importance of thorough checks. While we’re focusing on the technical complexities of the situation, it’s worth considering the parallel with the fascinating career of someone like Chita Rivera, whose key moments in her career showcase dedication and resilience in the face of challenges.
Ultimately, the thoroughness of these inspections will determine the future of the Boeing 737 Max 9 fleet.
The severity of the potential consequences directly correlates with the criticality of the affected component. For example, failures in critical control systems or structural elements can have severe safety implications.
Impact of Delays on Operations: Boeing 737 Max 9 Inspections Delayed
The prolonged inspections and subsequent delays of the Boeing 737 MAX 9 aircraft have far-reaching consequences for airline operations, passenger travel, and financial projections. These delays disrupt meticulously planned schedules, impacting passenger experiences and potentially straining airline resources. The cascading effect extends beyond the immediate operational issues, touching related industries and supply chains.The extended downtime of the 737 MAX 9 significantly impacts airline operations.
Flight schedules are altered, causing disruptions to connections and potentially affecting the entire network of a carrier. This translates to missed connections, inconvenienced passengers, and a negative impact on customer satisfaction.
Flight Schedules and Passenger Travel
Airline schedules are complex, finely-tuned networks designed to maximize efficiency and profitability. Delays in the 737 MAX 9 delivery and certification create ripples throughout these networks. A significant impact is seen in connecting flights, where delays in one leg often lead to cancellations or missed connections on subsequent flights. Airlines are forced to re-schedule flights, potentially impacting passenger plans and increasing the workload for customer service representatives.
Furthermore, passengers may face the inconvenience of rescheduling travel plans, potentially losing valuable time and incurring additional costs.
Financial Performance of Airlines
The financial implications of these delays are substantial. Airlines operating the 737 MAX 9 face reduced revenue streams due to grounded aircraft. Operational costs, such as crew salaries and maintenance expenses, continue, but revenue from cancelled or delayed flights does not materialize. Furthermore, airlines may be liable for compensation to passengers affected by cancellations or delays. This can lead to a significant decrease in profitability and potentially impact the overall financial health of the airline.
A real-world example of this is the impact on airlines that heavily relied on the 737 MAX fleet for a large portion of their routes.
Ripple Effects on Related Industries and Supply Chains
The delays in the 737 MAX 9 program extend beyond the airline industry. Suppliers of parts and services to Boeing and the airlines are affected. Reduced demand for certain components and expertise can lead to job losses and reduced production in related industries. For example, maintenance companies specializing in the 737 MAX may see reduced work orders, and component manufacturers may experience lower demand, impacting their production and workforce.
This disruption further emphasizes the interconnectedness of various industries and the cascading effect of delays in one area.
Potential Safety Concerns
The prolonged delays in inspections for the Boeing 737 MAX 9 raise legitimate safety concerns. While the manufacturer and regulatory bodies are diligently addressing these issues, the uncertainty surrounding the timeline and the potential scope of the necessary repairs introduce a layer of risk. Understanding the nature of these concerns and the established procedures for assessing them is crucial for maintaining public trust and safety.
Potential Impacts of Inspection Delays
The delays in inspections for the Boeing 737 MAX 9 could have several adverse effects on safety. A lack of timely maintenance could lead to the accumulation of damage or degradation of critical components, increasing the likelihood of malfunctions during flight. Furthermore, if the extent of required repairs is greater than anticipated, the potential for unforeseen complications during the repair process itself cannot be ignored.
This could impact the structural integrity and functionality of the aircraft, ultimately compromising its safety profile.
Evaluating Safety Risks Associated with Delays
Rigorous procedures are employed to assess the safety risks associated with these delays. These procedures typically involve a comprehensive review of the affected components, considering the potential consequences of any identified issues. Aircraft manufacturers often employ simulations and analyses to project the performance and behavior of the aircraft under various operational scenarios. Further, independent audits and evaluations from regulatory bodies are conducted to ensure that the safety standards are being met and that the repairs are effective.
These measures, while meticulous, do not eliminate the possibility of unexpected challenges or vulnerabilities arising from the extended downtime and repair procedures.
Comparison with Other Aircraft Models
Safety records of the 737 MAX 9 are being closely scrutinized in comparison to similar aircraft models. This analysis seeks to understand if the 737 MAX 9 exhibits any unique vulnerabilities or potential safety risks not observed in other models. Factors like design specifications, component materials, and maintenance procedures are compared to identify any potential disparities or emerging trends.
This comparative study aims to pinpoint any potential deviations from industry best practices or safety benchmarks. While direct comparisons are crucial, it’s also vital to recognize that each aircraft model, and its corresponding maintenance history, is unique.
Safety Procedures for Delayed Aircraft
Safety procedures for aircraft with delayed inspections are well-defined and meticulously followed. These include restrictions on operational use, stringent pre-flight checks, and additional inspections conducted by qualified personnel. The severity of the delay and the identified safety concerns will dictate the specific procedures and restrictions. This approach prioritizes safety by minimizing operational risks until the inspections are completed and the aircraft is deemed safe for flight.
For example, additional ground tests, flight simulations, and expert reviews might be implemented before the aircraft is cleared for service.
Regulatory Responses and Actions
The delayed inspections of Boeing 737 MAX 9 aircraft highlight the critical role of regulatory bodies in ensuring aviation safety. Regulatory scrutiny and subsequent actions often serve as a crucial deterrent against potential safety hazards and contribute to a culture of accountability within the aviation industry. These responses are not merely reactive; they are integral components of maintaining public trust and upholding the highest standards of airworthiness.The FAA, along with other international aviation authorities, play a vital role in enforcing safety regulations and standards for commercial aircraft.
The delayed inspections on the Boeing 737 Max 9 are definitely a headache, but it’s worth considering the broader economic ripples. For example, the impact of a potential Palestinian state on the German economy is a fascinating area of study. palestinian state german economy could be significantly affected by various factors, including trade agreements and regional stability.
Ultimately, these complex global issues all intertwine, and the delayed inspections highlight just how interconnected everything really is.
Their responses to delays in inspections, along with Boeing’s actions to rectify the situation, are closely monitored by industry stakeholders, passengers, and the public.
FAA Actions and Investigations
The Federal Aviation Administration (FAA) is responsible for overseeing the safety of civil aviation in the United States. In response to the delays, the FAA likely initiated investigations to determine the root cause of the delays, assess the potential impact on safety, and verify that Boeing’s corrective actions are adequate. These investigations may include reviewing Boeing’s engineering documentation, inspecting the aircraft, and interviewing personnel involved in the production and maintenance process.
Boeing’s Corrective Actions
Boeing’s response to the delays is crucial in regaining public trust and maintaining its reputation. Boeing likely implemented corrective actions to address the issues causing the delays. These actions may include improved manufacturing processes, enhanced quality control measures, or additional training for maintenance personnel. The effectiveness of these corrective actions will be subject to ongoing scrutiny and verification by the FAA and other regulatory bodies.
Potential Penalties and Sanctions
Potential penalties or sanctions for Boeing or airlines due to the delays are dependent on the severity of the issues and the regulatory framework in place. These penalties may range from fines to the grounding of specific aircraft or even the imposition of operational restrictions. The potential penalties could vary significantly depending on the specific violations and the nature of the delays.
Past instances of similar issues in the aviation industry, such as engine malfunctions or design flaws, have resulted in substantial penalties, grounding of aircraft, and reputational damage for the involved parties. For example, if significant safety concerns are confirmed and deemed a violation of established safety standards, substantial financial penalties and operational restrictions are plausible.
Future Implications and Solutions
The Boeing 737 MAX 9 inspection delays highlight systemic issues within the aviation industry, potentially impacting safety and financial stability. Understanding these implications and implementing proactive solutions is crucial for maintaining public trust and ensuring future safety. Prolonged delays can cascade into significant repercussions, affecting not only Boeing but the entire aviation ecosystem.
Potential Long-Term Implications
The prolonged delays in 737 MAX 9 inspections have far-reaching implications. Reduced production capacity leads to lost revenue for Boeing, impacting investor confidence and potentially impacting job security. Furthermore, airlines reliant on these planes face schedule disruptions and operational inefficiencies, potentially impacting their bottom lines. The negative publicity associated with these delays can damage the overall perception of aviation safety and hinder the industry’s ability to attract and retain skilled personnel.
Strategies for Preventing Similar Delays
Several strategies can help prevent future delays. Improved communication channels between manufacturers, regulatory bodies, and airlines are essential. Clearer, more detailed inspection procedures, readily accessible to all parties, would minimize ambiguity and streamline the process. A robust system of quality control, including independent audits and rigorous testing, is vital. Investing in advanced inspection technologies and training personnel in their use can also expedite the process and reduce potential errors.
Best Practices in Aircraft Maintenance and Inspection
Implementing best practices in maintenance and inspection is paramount. Comprehensive documentation of every inspection, including detailed records of findings and corrective actions, is crucial. Standardized procedures and training programs for maintenance personnel ensure consistent and high-quality work. Proactive maintenance schedules, based on rigorous analysis of flight data and component usage, can predict potential issues before they escalate.
Continuous monitoring of emerging technologies and their application in maintenance and inspection procedures is also critical.
Comparison of Inspection Procedures
Aircraft Model | Inspection Frequency | Inspection Criteria |
---|---|---|
Boeing 787 Dreamliner | Annually | Comprehensive review of all systems, with specific focus on critical components. |
Airbus A320neo | Quarterly | Focus on critical components and systems, with an emphasis on early detection of potential issues. |
Boeing 737 MAX 9 | Previously, monthly; now subject to review and revision. | Focus on areas identified as needing more thorough inspection due to previous issues. |
Solutions to Address the Delays
A structured approach to resolving the delays is crucial. The following solutions are vital:
- Enhanced Communication Protocols: Establishing a clear communication channel between Boeing, regulatory bodies, and airlines is essential to expedite the approval process and provide real-time updates on inspection progress.
- Comprehensive Inspection Procedures: Re-evaluating and refining inspection procedures to address identified weaknesses is paramount. This includes incorporating advanced technologies to detect anomalies earlier.
- Robust Quality Control Mechanisms: Implementing robust quality control measures, such as independent audits and rigorous testing, to ensure adherence to standards and prevent recurrence of similar issues.
- Investment in Advanced Technologies: Investing in advanced inspection technologies, such as AI-powered diagnostics and predictive maintenance systems, to identify potential problems proactively. This would significantly reduce the time and resources required for inspections.
- Dedicated Training Programs: Implementing comprehensive training programs for maintenance personnel to ensure that they are equipped with the latest knowledge and expertise to perform inspections effectively and efficiently.
Illustrative Case Studies
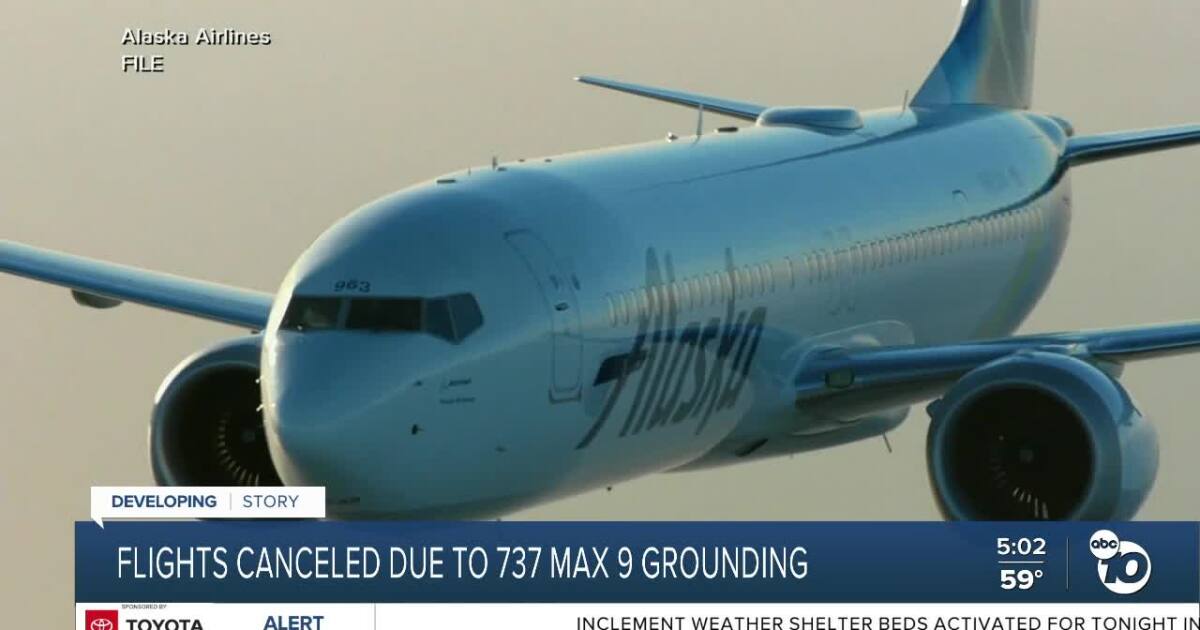
Delayed inspections on the Boeing 737 MAX 9 highlight the intricate interplay between safety protocols, maintenance schedules, and operational efficiency. Understanding past cases of inspection processes, both successful and flawed, is crucial in assessing the current situation and anticipating potential future challenges. Analyzing the methodology behind these inspections allows for a more comprehensive understanding of the data and its implications.
Inspection Process Case Study: A Successful Inspection of a Boeing 737-800
A thorough inspection of a Boeing 737-800 aircraft, a comparable model to the MAX 9, demonstrated the effectiveness of a standardized inspection process. The inspection, conducted at a certified maintenance facility, adhered to rigorous guidelines Artikeld by the FAA and Boeing. Inspection checklists were meticulously followed, documenting all findings, including any discrepancies or repairs required. A dedicated team of qualified technicians used advanced diagnostic tools and techniques, such as ultrasonic testing and visual examinations.
The methodology ensured a comprehensive evaluation of critical components, contributing to the safe operation of the aircraft.
Potential Incident Related to Delayed Inspections
A potential incident involving a delayed inspection of a Boeing 737 MAX 9 highlights the potential ramifications of inadequate maintenance. Let’s consider a scenario where routine inspections, crucial for identifying potential structural weaknesses, were postponed due to staffing shortages and logistical constraints.
Sequence of Events:
- A 737 MAX 9 aircraft experiences a gradual deterioration in a critical component, such as a wing spar or fuselage section, due to fatigue and stress. The gradual deterioration is not detected during routine visual checks.
- Subsequent inspections, delayed by several months due to scheduling issues, fail to catch the growing damage. The damage has progressed to a critical level.
- During a flight, the affected component suddenly fails, resulting in a catastrophic structural failure.
- The aircraft experiences an unexpected and severe aerodynamic event, leading to a loss of control. The crew struggles to maintain control.
- The flight crew implements emergency procedures, but the damage is beyond repair.
- The aircraft is forced to make an emergency landing, potentially resulting in injuries to passengers and crew, and significant damage to the aircraft.
Outcomes:
- Significant loss of life and injuries are possible, depending on the severity and suddenness of the structural failure.
- The airline faces significant financial losses due to the aircraft damage, operational disruption, and potential legal liabilities.
- The incident triggers a comprehensive investigation, potentially revealing deficiencies in the inspection process and the overall maintenance program.
- The FAA and regulatory bodies will likely impose stringent corrective actions to prevent similar incidents in the future.
Closing Summary
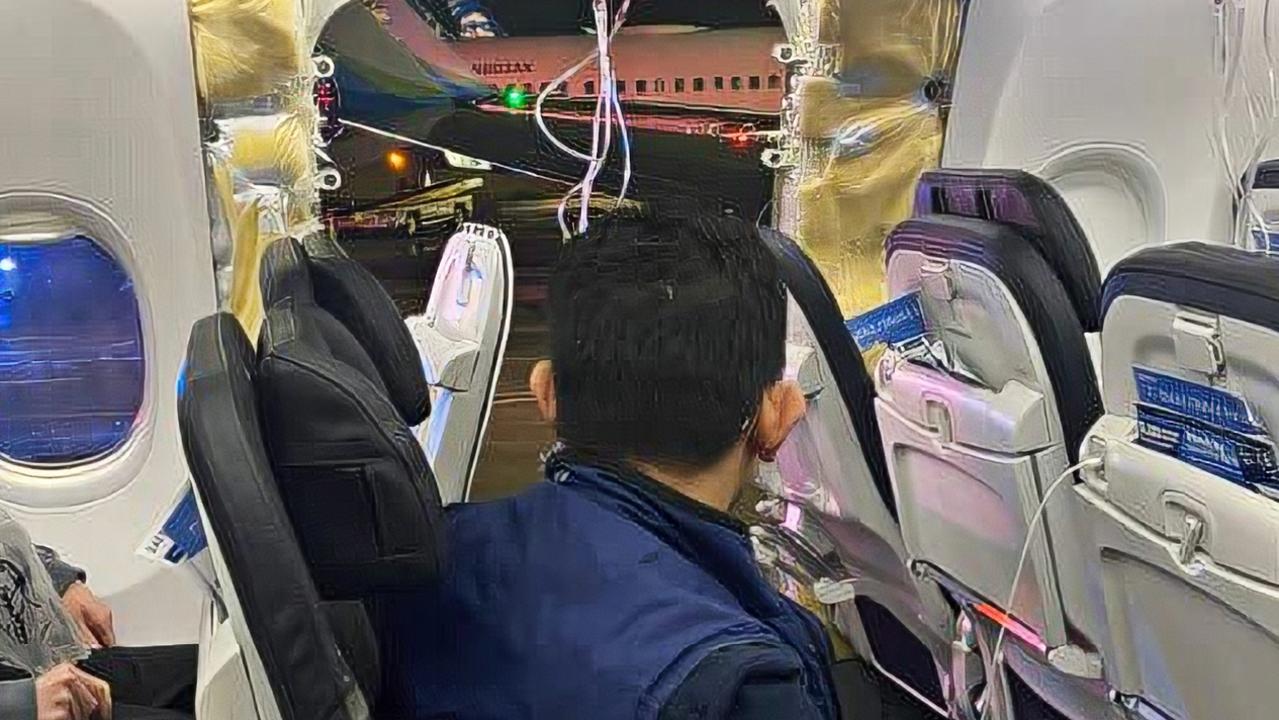
The delays in inspections for the Boeing 737 MAX 9 underscore the critical need for robust and proactive maintenance protocols. This incident serves as a stark reminder of the interconnectedness of the aviation industry and the cascading effects of delays. Ultimately, ensuring the safety and reliability of aircraft is paramount, demanding transparent communication and effective solutions from all stakeholders involved.
Answers to Common Questions
What are the primary reasons for the inspection delays?
The delays are likely due to a combination of factors, including complex inspection procedures, potential component defects, and the need for rigorous testing and verification. Further details remain undisclosed at this time.
What is the impact on airline operations?
The delays lead to disruptions in flight schedules, potentially impacting passenger travel plans and revenue projections for airlines. Ripple effects extend to related industries and supply chains.
What are the potential safety concerns?
Uncertainties surrounding the delayed inspections naturally raise safety concerns. Rigorous evaluations of the potential risks and thorough inspections are crucial to mitigating these risks.
What steps is Boeing taking to address the issues?
Boeing is likely taking steps to address the issues and ensure the safety of the aircraft, including investigating the delays, rectifying any potential issues, and collaborating with regulators.