
Boeing 737 Max Bolts A Deep Dive
Boeing 737 Max bolts: a crucial yet often overlooked aspect of aviation safety. This in-depth exploration delves into the historical context, manufacturing processes, maintenance, potential failures, design considerations, and regulatory requirements surrounding these seemingly simple components. Understanding their significance is paramount to appreciating the complexity and precision inherent in aircraft engineering.
From the initial design stages to ongoing maintenance, every aspect of bolt selection, production, and inspection plays a vital role in ensuring the structural integrity and safety of the 737 Max. This exploration will cover the entire lifecycle of these bolts, from the raw materials to their ultimate role in supporting the aircraft’s structure.
Historical Context of Boeing 737 MAX Bolts
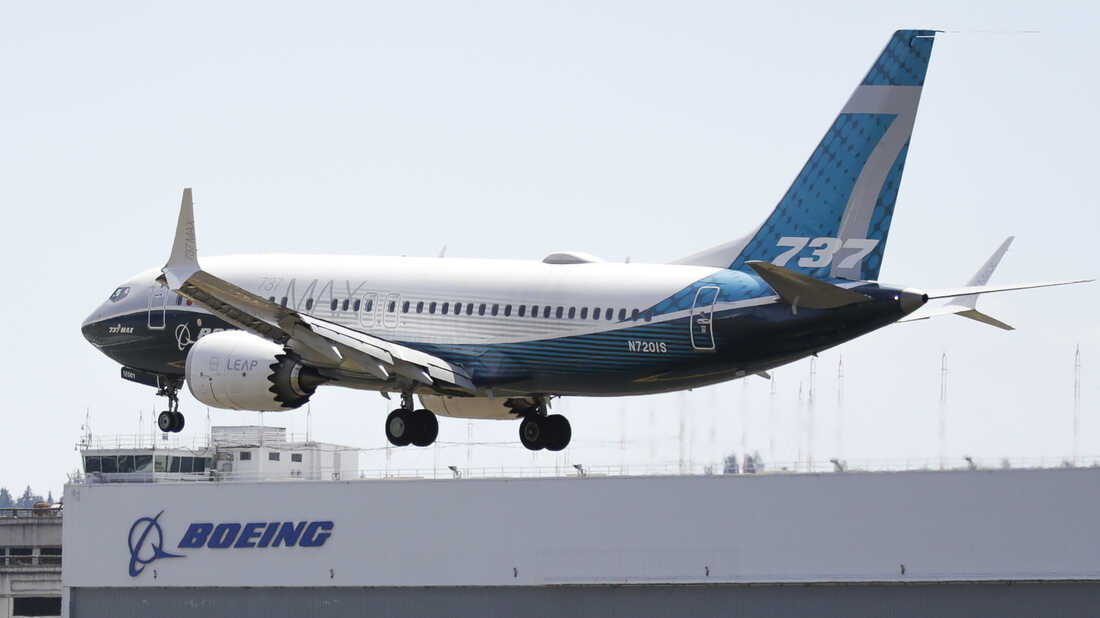
The Boeing 737 MAX, a crucial model in the airline industry, has faced scrutiny and scrutiny concerning its bolts. Understanding the history of bolt usage is vital to comprehending the intricacies of the design, production, and maintenance processes. This analysis delves into the evolution of bolts in the 737 MAX, examining the different types used, production timelines, and maintenance procedures.The 737 MAX’s design incorporates a complex network of bolts that hold the aircraft together.
Understanding their history, materials, and specifications is essential for both maintenance and potential future upgrades. This detailed examination clarifies the specific bolts used in various 737 MAX iterations and their relation to the overall aircraft design.
The Boeing 737 Max bolts, a seemingly simple part, have been a source of significant debate and controversy. Recent events, like the ongoing California State University system faculty strike ( california state university system faculty strike ), highlight the ripple effect of complex issues, even those seemingly isolated to an engineering problem. Ultimately, the 737 Max bolts, in the larger context, serve as a reminder of the potential for broader consequences in industrial and societal systems.
Timeline of Boeing 737 MAX Production and Bolt Usage
The Boeing 737 MAX program has a production timeline marked by various phases and significant events. This section Artikels key periods of production and their relation to bolt usage. The initial design phase, the production ramp-up, and the subsequent modifications illustrate how bolt specifications and maintenance procedures have adapted over time. For instance, the design process often incorporates iterative adjustments based on operational feedback, including modifications related to bolt strength and durability.
The Boeing 737 Max bolts, a critical component in the aircraft’s structure, have been a major talking point in recent aviation news. However, the ongoing political climate in Taiwan, particularly the upcoming election with candidate Lai Ching-te, taiwan election china lai ching te , is also generating significant buzz. Ultimately, the safety of these bolts and the broader implications for air travel remain top-of-mind concerns for aviation enthusiasts and experts alike.
Different Types of Bolts Used in the 737 MAX
The 737 MAX employs a diverse range of bolts, each with specific applications and materials. Different sections of the aircraft necessitate various bolt types, depending on the load-bearing requirements and environmental factors.
- Structural bolts, typically made of high-strength steel alloys, secure the wings, fuselage, and other load-bearing components.
- Fasteners for engine mounts and other critical systems use specific alloys to ensure high tensile strength and resistance to fatigue.
- Connection bolts for interior components, like panels and fixtures, often use corrosion-resistant materials like stainless steel.
Evolution of Fastening Techniques
The evolution of fastening techniques has profoundly influenced the 737 MAX’s design. Modern methods incorporate enhanced quality control measures and more precise manufacturing techniques. The adoption of advanced materials and processes has led to improvements in strength, durability, and overall safety. Examples include the use of advanced fastener inspection technologies that have been adopted.
Documented History of 737 MAX Bolt Maintenance Procedures
Maintenance procedures for bolts on the 737 MAX have evolved over time. Initial procedures were developed based on the aircraft’s design and the available technology. Ongoing updates and revisions reflect lessons learned from operational experiences and advancements in engineering knowledge. Regular inspections, torque checks, and replacement schedules are crucial components of maintenance.
Comparison of Bolt Types in Previous 737 Models and the 737 MAX
The following table compares the bolt types used in previous 737 models with those employed in the 737 MAX. Note that specific materials and specifications may vary depending on the precise model and component.
Bolt Type | Previous 737 Models | 737 MAX |
---|---|---|
Wing Attachment Bolts | Steel alloy, standard specifications | High-strength titanium alloy, enhanced specifications for fatigue resistance |
Engine Mount Bolts | Steel alloy, standard specifications | Nickel-based alloy, improved thermal conductivity and strength |
Interior Panel Bolts | Steel alloy, various specifications based on application | Stainless steel, enhanced corrosion resistance |
Manufacturing Processes and Bolt Selection
The Boeing 737 MAX, like any sophisticated aircraft, relies heavily on the precision and integrity of its fasteners. Understanding the manufacturing processes and selection criteria for bolts is crucial to ensuring the structural safety and longevity of the aircraft. From the raw materials to the final inspection, each step plays a critical role in the overall performance of the plane.
This section delves into the meticulous processes involved in producing and selecting the bolts that hold the 737 MAX together.Bolt selection and manufacturing are not arbitrary processes. The rigorous standards applied ensure that every bolt meets the stringent requirements for the specific application within the 737 MAX’s complex structure. The selection process involves careful consideration of material properties, expected loads, and environmental conditions to which the bolt will be exposed.
Material Sourcing and Quality Control
The selection of materials for 737 MAX bolts is a critical aspect of the manufacturing process. High-strength steel alloys, often with specific heat treatments, are commonly used to achieve the necessary tensile strength and fatigue resistance. Suppliers are rigorously vetted to ensure the consistency and quality of the raw material. This involves detailed metallurgical analysis, chemical composition verification, and extensive testing of the material’s mechanical properties.
Furthermore, the quality control procedures are meticulously documented and regularly audited to maintain the highest standards throughout the entire process.
Bolt Type Selection Criteria
Different types of bolts are selected for various components based on their specific requirements. Factors like the expected tensile loads, vibration levels, and environmental conditions influence the choice of material and thread type. For example, bolts in high-stress areas, like wing structures or landing gear, would require higher strength and fatigue resistance compared to those in less demanding areas.
The selection process is guided by engineering specifications and ensures that each bolt can withstand the anticipated loads throughout the aircraft’s operational life. The choice of bolt type also takes into account factors such as corrosion resistance, and compatibility with other materials in the assembly.
Torque Specifications and Impact on Integrity, Boeing 737 max bolts
Torque specifications are critical to the integrity of the aircraft structure. Proper tightening ensures the bolts develop the necessary clamping force to hold components securely together. Improper torque can lead to loosening, fatigue failure, and ultimately catastrophic structural failure. Torque specifications are meticulously determined through extensive simulations and testing. These specifications are documented in detailed procedures, and followed strictly during assembly.
Testing and Inspection Procedures
Rigorous testing and inspection procedures are implemented throughout the bolt manufacturing process. This ensures that every bolt meets the stringent quality standards required for the 737 MAX. Testing procedures encompass various stages, including tensile testing, fatigue testing, and visual inspection. These tests are performed by qualified personnel, following established protocols and documented procedures, using sophisticated equipment to ensure precise measurement.
The results are meticulously recorded and analyzed to confirm the bolt’s compliance with the required specifications.
Bolt Production and Quality Check Stages
Stage | Process | Quality Check |
---|---|---|
Raw Material Inspection | Verification of material composition and mechanical properties | Chemical analysis, tensile testing, and visual inspection |
Bolt Manufacturing | Precision machining and shaping of bolts | Dimensional inspection, thread profile verification, and surface finish assessment |
Heat Treatment (if applicable) | Improving the strength and durability of the bolt | Hardness testing, microstructure analysis, and dimensional checks after heat treatment |
Final Inspection | Verification of dimensions, surface quality, and mechanical properties | Visual inspection, dimensional measurements, and mechanical testing |
Packaging and Storage | Proper packaging and storage of finished bolts | Documentation of batch details, traceability, and compliance with storage guidelines |
Maintenance and Inspection of Boeing 737 MAX Bolts
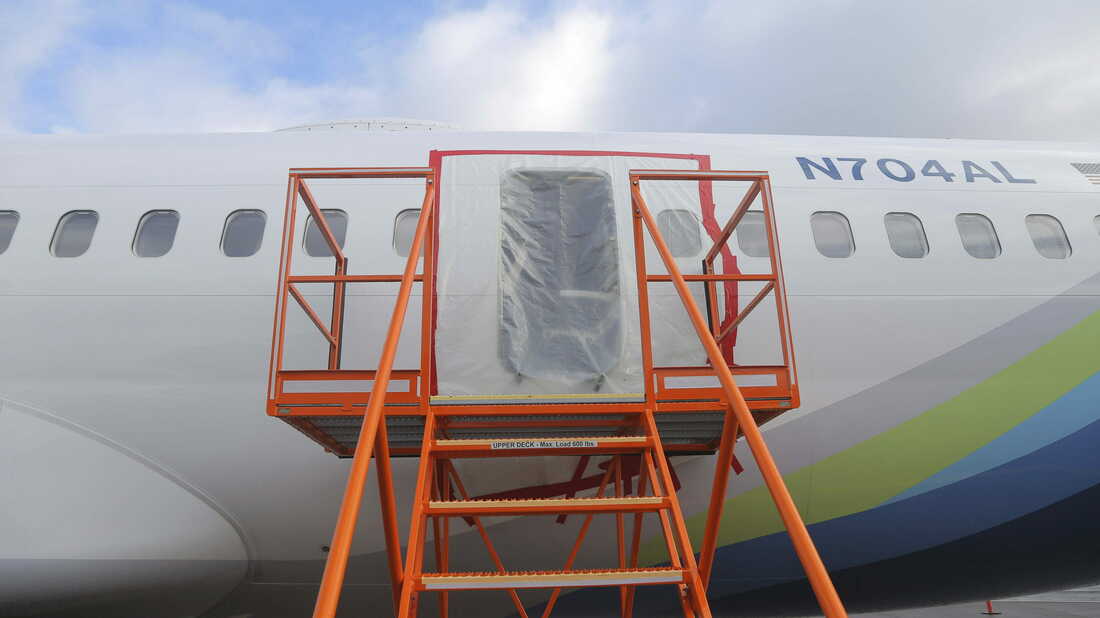
Maintaining the integrity of the Boeing 737 MAX’s numerous bolts is crucial for aircraft safety and operational reliability. Proper maintenance schedules and inspection procedures are essential to detect potential issues early, preventing catastrophic failures and ensuring the aircraft’s structural integrity. This section details the recommended maintenance practices for bolts on the 737 MAX, highlighting inspection methods and procedures for replacing or repairing damaged components.The Boeing 737 MAX’s complex structure relies heavily on the integrity of its bolts.
Failure of a single bolt, if not detected and addressed promptly, can lead to significant structural issues, impacting the aircraft’s stability and safety. The recommended maintenance and inspection procedures aim to prevent such failures.
Recommended Maintenance Schedules
Scheduled maintenance schedules for bolts on the 737 MAX are developed based on flight cycles, accumulated time, and operational conditions. These schedules ensure proactive identification and management of potential bolt issues. Adherence to these schedules is critical to maintain the aircraft’s structural integrity.
Methods for Identifying Potential Issues
Visual inspections are a fundamental aspect of bolt maintenance. Trained personnel visually inspect bolts for signs of damage, corrosion, or deformation. Non-destructive testing (NDT) methods are also employed to further assess bolt integrity. These techniques can detect hidden flaws that visual inspections might miss.
Visual Inspections
Visual inspections typically involve careful examination of the bolt head, shank, and any threads for signs of damage, corrosion, deformation, or wear. This process necessitates detailed checklists and established criteria for acceptable conditions.
Non-Destructive Testing (NDT)
NDT methods such as magnetic particle inspection (MPI) or ultrasonic testing (UT) can detect subsurface flaws and cracks that are not visible to the naked eye. These techniques are particularly useful for assessing the integrity of critical bolts.
Procedures for Replacing or Repairing Damaged Bolts
Damaged bolts are replaced according to established procedures. The replacement process involves removing the damaged bolt, inspecting the mating threads and surfaces, and installing a new bolt of the correct specifications. Detailed procedures ensure consistency and safety.
Potential Impact of Corrosion
Corrosion can significantly compromise the structural integrity of bolts. Environmental factors, such as humidity and exposure to chemicals, can accelerate corrosion. The impact of corrosion on bolt integrity can vary, leading to reduced tensile strength, fatigue, and premature failure. Corrosion can also make visual inspection more difficult, potentially masking damage.
Speaking of safety concerns, the recent cancellation of the Indiana University Samia Halaby exhibition, focusing on aviation safety, has got me thinking about the Boeing 737 Max bolts. It seems like a strange coincidence, doesn’t it? Maybe the focus on safety in general is being shifted away from the 737 Max bolts, given the ongoing investigations and debates surrounding the plane’s design.
Maybe it’s all connected? You can read more about the exhibition cancellation here. Regardless, the whole thing highlights the complex web of factors surrounding airplane safety, and the importance of thorough investigations, like the ones surrounding the Boeing 737 Max bolts.
Inspection Points During Scheduled Maintenance
Inspection Point | Description | Frequency |
---|---|---|
Bolt Head | Inspect for cracks, deformation, or corrosion | Every 100 flight cycles |
Bolt Shank | Examine for cracks, corrosion, or signs of wear | Every 500 flight cycles |
Bolt Threads | Inspect for damage, stripping, or corrosion | Every 250 flight cycles |
Mating Surfaces | Assess for corrosion, galling, or wear | Every 100 flight cycles |
Bolt Failures and Their Consequences
The Boeing 737 MAX, like any complex aircraft, relies on a vast network of meticulously engineered components, including bolts. These seemingly small fasteners play a crucial role in maintaining the structural integrity of the aircraft, and their failure can have severe consequences. Understanding the potential causes, impacts, and preventative measures associated with bolt failures is essential for ensuring aviation safety.Bolt failures in the 737 MAX, as in any aircraft, can stem from various underlying issues.
Material defects, fatigue, improper installation, and environmental factors can all contribute to compromised fastener integrity. These failures, though often seemingly minor, can have cascading effects on the overall structural integrity of the aircraft, potentially leading to catastrophic outcomes.
Common Causes of Bolt Failures
Bolt failures are often the result of a combination of factors. Material defects, such as inconsistencies in the metal’s composition or manufacturing process, can compromise a bolt’s inherent strength. Over time, repeated stress and strain on the bolt, a phenomenon known as fatigue, can lead to microscopic cracks that weaken the material and ultimately cause failure. Furthermore, improper installation procedures, such as insufficient tightening torque or incorrect alignment, can create stress concentrations that exacerbate the risk of failure.
Consequences of Bolt Failures on Structural Integrity
Bolt failures can have profound implications for the structural integrity of the 737 MAX. A single failed bolt can compromise the integrity of a critical joint, potentially leading to the propagation of damage throughout the aircraft’s structure. This progressive failure can impact the stability of the aircraft during flight, potentially leading to loss of control or catastrophic structural collapse.
The consequences can range from minor malfunctions to severe structural damage, emphasizing the critical importance of preventive measures.
Safety Implications of Bolt Failures
The safety implications of bolt failures are substantial. A compromised fastener can directly affect the aircraft’s ability to withstand the stresses of flight. This can lead to unpredictable and potentially catastrophic outcomes, affecting passengers, crew, and the surrounding environment. This highlights the need for stringent quality control measures during manufacturing and rigorous maintenance protocols to mitigate the risk of such failures.
Preventive Measures to Mitigate Bolt Failures
Rigorous quality control measures are essential during the manufacturing process. These include material testing, stringent quality checks, and precise manufacturing tolerances to ensure the quality and consistency of bolts. Thorough maintenance and inspection procedures, including regular visual inspections, torque checks, and the use of non-destructive testing methods, are crucial to identify and address potential issues early on. Furthermore, continuous monitoring and analysis of flight data can help to identify potential patterns and trends related to bolt failures, enabling proactive measures to be implemented.
Categorization of Bolt Failures and Their Impact
Type of Bolt Failure | Potential Impact |
---|---|
Material defects (e.g., cracks, inclusions) | Compromised structural integrity, potential for sudden catastrophic failure |
Fatigue cracks | Progressive damage, reduced load-bearing capacity, potential for failure under operational stress |
Improper installation (e.g., incorrect torque) | Stress concentrations, premature failure, potential for damage propagation |
Environmental degradation (e.g., corrosion) | Reduced strength, increased susceptibility to failure, often progressive damage |
Importance of Proper Maintenance and Inspection
Regular and thorough maintenance and inspection procedures are vital in preventing bolt failures. These procedures should include detailed visual inspections for signs of damage, corrosion, or wear. Torque checks should be conducted according to prescribed standards, and non-destructive testing methods, such as ultrasonic testing, should be used to identify hidden defects. These preventative measures are crucial to ensure the longevity and safety of the 737 MAX fleet.
Design and Engineering Considerations for 737 MAX Bolts
The meticulous selection and application of bolts are critical to the structural integrity and longevity of the Boeing 737 MAX. This section delves into the engineering considerations behind choosing the appropriate bolt types, sizes, and materials for this complex aircraft. Understanding these factors is crucial for ensuring both safety and efficiency throughout the aircraft’s operational life.Careful consideration must be given to the intricate interplay between bolt characteristics and the specific stresses they will endure within the 737 MAX’s complex structure.
This includes understanding the forces, vibrations, and environmental conditions the bolts will face during flight and maintenance. Bolt selection and design modifications directly influence the aircraft’s overall performance and safety.
Stress Analysis and Load Calculations
Accurate stress analysis is paramount in selecting appropriate bolts. Engineers meticulously analyze the forces exerted on each bolt connection throughout the aircraft’s lifespan, from takeoff and landing to cruising altitudes. These analyses incorporate various factors, including aerodynamic forces, engine thrust, and weight distribution. Load calculations are performed using sophisticated Finite Element Analysis (FEA) software, which allows engineers to model the stress distribution across complex geometries and identify potential stress concentrations.
This detailed understanding ensures the bolts can withstand the predicted loads without yielding or fracturing. Examples of such analyses include evaluating the stress on wing attach points during maneuvering and landing gear deployment.
Impact of Design Modifications on Bolt Requirements
Design modifications of the 737 MAX, such as alterations to wing structures or engine mounts, necessitate a reassessment of bolt requirements. Changes in geometry, load paths, or operating conditions directly impact the stresses on the bolts. Engineers must conduct comprehensive stress analysis for the modified design to ensure the new bolt configuration can reliably handle the expected loads.
For example, if the wing design is altered, the stress on the bolts connecting the wing to the fuselage will likely change, requiring new calculations and possibly different bolt types.
Comparison of Different Bolt Types
Different bolt types exhibit varying performance characteristics under diverse conditions. The selection depends on factors like tensile strength, yield strength, fatigue life, corrosion resistance, and cost. High-strength steel bolts are frequently used for their exceptional tensile strength. Stainless steel bolts might be preferred in environments with high corrosion risk. Titanium alloys are an option for applications requiring light weight and high strength.
Role of Simulations in Evaluating Bolt Performance
Simulations play a vital role in evaluating bolt performance in the 737 MAX design. Computer simulations, particularly FEA, allow engineers to virtually test the bolts under various load conditions and identify potential failure points before physical prototypes are built. This approach significantly reduces design costs and minimizes the risk of costly errors during manufacturing or operation. By virtually testing numerous scenarios, such as extreme weather conditions and high-stress situations, engineers can predict how the bolts will perform and adjust designs accordingly.
The Boeing 737 Max bolts, a significant safety concern, have dominated headlines lately. While those issues continue to be a major focus, it’s interesting to see how the Emmy Awards TV ratings are trending this year, which could reflect broader viewing habits. A closer look at the emmy awards tv ratings might provide some insight into the entertainment industry’s current appeal.
Ultimately, the 737 Max bolt situation highlights the crucial importance of thorough safety checks in the aviation industry.
Comparison of Bolt Types
Bolt Type | Tensile Strength (MPa) | Yield Strength (MPa) | Fatigue Life (cycles) |
---|---|---|---|
High-Strength Steel | >1200 | >800 | >106 |
Stainless Steel | >900 | >600 | >5 x 105 |
Titanium Alloy | >900 | >600 | >106 |
The table above presents a simplified comparison. Actual values can vary significantly based on specific bolt grades, manufacturing processes, and environmental factors. Engineers must consult material datasheets and perform detailed analyses to make informed selections.
Regulatory Requirements and Standards for 737 MAX Bolts
The Boeing 737 MAX program, while ultimately a success story in terms of design and efficiency, was significantly impacted by the events surrounding the 2018-2019 incidents. A critical component of any successful and safe aviation project is adherence to rigorous regulatory frameworks. Understanding these regulations, the associated standards, and the enforcement mechanisms is paramount to ensuring the structural integrity and safety of the aircraft.The safety of air travel hinges on a complex web of regulations and standards that meticulously govern every aspect of aircraft design, manufacture, operation, and maintenance.
This includes the specific requirements for materials, components, and procedures, such as those pertaining to bolts, a seemingly simple but crucial element.
Relevant Aviation Regulations and Standards
Aircraft bolts are subject to a multitude of regulations and standards, stemming from both international and national bodies. These regulations address everything from the material specifications and manufacturing processes to the procedures for inspection and maintenance. The specific requirements are detailed in numerous documents and standards, and their adherence is essential for safety.
Procedures for Compliance with Regulations
Compliance with these regulations involves a structured approach. Manufacturers must meticulously document every step of the bolt production process, from raw material procurement to final inspection. Detailed records must be kept, outlining the specific standards followed and the results of each inspection. Thorough documentation is critical for demonstrating adherence to regulations and for facilitating audits. This ensures traceability and allows for effective verification of compliance at all stages.
Organizations Responsible for Enforcing Regulations
Several organizations play a vital role in enforcing these regulations. These include national aviation authorities, such as the FAA (Federal Aviation Administration) in the United States and equivalent bodies in other countries. International organizations, like the ICAO (International Civil Aviation Organization), also contribute to setting global standards and ensuring their adherence.
The Boeing 737 Max bolts, a seemingly mundane engineering detail, take on a different dimension when you consider the human stories behind them. Thinking about the intricate safety protocols and meticulous engineering behind these critical components, I was reminded of the powerful resilience displayed by Holocaust survivor portraits, like those by Gillian Laub holocaust survivor portraits gillian laub.
These portraits, each a testament to enduring human spirit, are a poignant counterpoint to the complex and often fraught world of modern aviation, especially when considering the safety issues surrounding the Boeing 737 Max.
Key Regulatory Requirements for Bolts in Aircraft
Regulatory Requirement | Description |
---|---|
Material Specifications | Bolts must be manufactured from materials with specific properties, including tensile strength, yield strength, and elongation, as defined in standards like ASTM (American Society for Testing and Materials). |
Manufacturing Processes | The manufacturing process must conform to rigorous quality control standards, ensuring consistent quality and dimensional accuracy. |
Dimensional Tolerances | Bolts must adhere to precise dimensional tolerances to ensure proper fit and function within the aircraft structure. |
Surface Treatments | Surface treatments, if any, must meet specific requirements to prevent corrosion and maintain structural integrity. |
Proof Testing | Bolts must undergo proof testing to verify their strength and resistance to failure under expected load conditions. |
Inspection Procedures | Specific inspection procedures must be followed throughout the manufacturing process and during maintenance, including visual, dimensional, and destructive testing. |
Role of Certification Processes in Ensuring Bolt Quality
Certification processes are integral to the entire process. Certification bodies validate that the manufacturer’s processes and procedures meet the regulatory requirements. This involves audits of the manufacturing facility, verification of materials and processes, and review of the documentation. The certification process ensures that the bolts used in aircraft meet the highest safety standards, mitigating potential risks. These certifications demonstrate a commitment to quality and safety, and this is essential to maintaining public trust in the aviation industry.
Closing Notes
In conclusion, the Boeing 737 Max bolt system is a testament to meticulous engineering and rigorous quality control. The intricate interplay of historical context, manufacturing processes, maintenance procedures, and regulatory standards all contribute to the safety and reliability of this critical component. Understanding these details underscores the importance of thorough inspections and maintenance, ultimately safeguarding the integrity of the aircraft and its passengers.
FAQ Guide
What are the common causes of bolt failures in the 737 Max?
Common causes include material defects, fatigue from repeated stress cycles, improper torque application during assembly, and corrosion. Additionally, issues with the manufacturing process or improper maintenance can contribute to these failures.
What are the regulatory standards for using bolts in aircraft construction?
Specific aviation regulations and standards dictate the materials, specifications, and manufacturing processes for aircraft bolts. These standards are designed to ensure the highest level of safety and performance. Different organizations, like the FAA and EASA, play a role in enforcing and overseeing these regulations.
How are bolts inspected during the 737 Max maintenance process?
Visual inspections, non-destructive testing methods (like ultrasonic testing), and torque checks are common procedures. The frequency and type of inspection depend on the specific location and function of the bolt.
What is the impact of corrosion on bolt integrity?
Corrosion can weaken bolts, reducing their tensile strength and fatigue life. This can compromise the structural integrity of the aircraft, leading to potential failures. Proper preventative maintenance and protective coatings are crucial to mitigate the impact of corrosion.